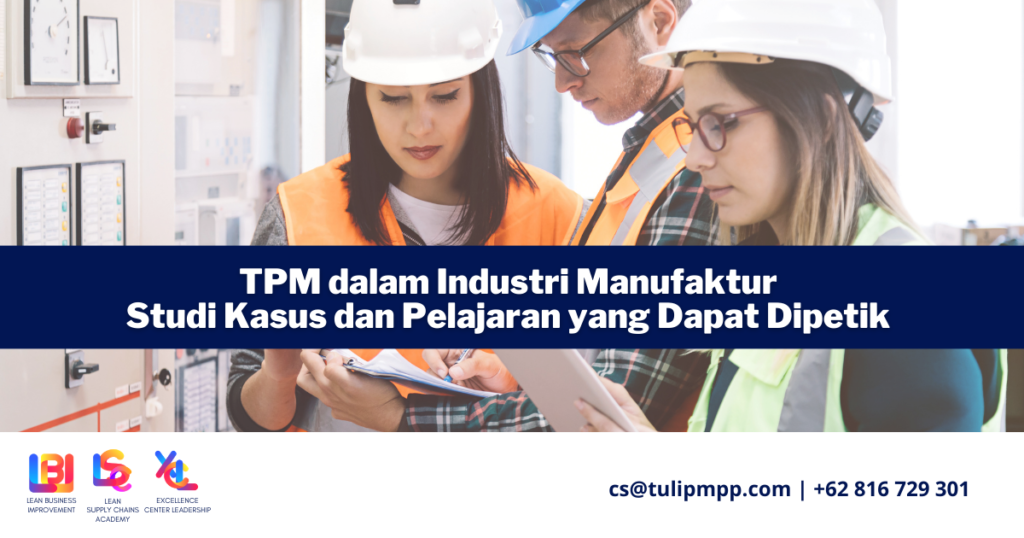
TPM dalam Industri Manufaktur, Studi Kasus dan Pelajaran yang Dapat Dipetik. Dan kita akan kaitkan dalam bahasan manfaat Nyata Implementasi Sukses TPM sudah terbukti di banyak perusahaan. Dan kali ini saya ingin berbagi cerita dan kasus bisnis yang saya percaya bisa membantu Anda dalam menerapkan TPM di perusahaan tempat Anda bekerja.
Manfaat Nyata Implementasi Sukses TPM
Total Productive Maintenance (TPM) adalah suatu konsep perawatan dan peningkatan produktivitas dalam industri manufaktur yang melibatkan seluruh karyawan. Berikut ini adalah 7 manfaat dari penerapan TPM yang sukses bagi industri manufaktur:
- Penurunan downtime: Toyota, perusahaan otomotif terkemuka asal Jepang, berhasil mengurangi downtime mesinnya hingga 90% setelah menerapkan TPM. Dengan demikian, mereka mampu meningkatkan kapasitas produksi mobil mereka secara signifikan.
- Peningkatan efisiensi produksi: Unilever, salah satu perusahaan FMCG (Fast Moving Consumer Goods) terbesar di dunia, melaporkan peningkatan efisiensi produksi sebesar 30% setelah menerapkan TPM di beberapa pabrik mereka.
- Pengurangan biaya perawatan: Samsung, perusahaan elektronik raksasa asal Korea Selatan, berhasil mengurangi biaya perawatan mesinnya sebesar 40% setelah menerapkan TPM, sehingga dapat meningkatkan daya saing perusahaan dalam pasar global.
- Peningkatan kualitas produk: Nestlé, perusahaan makanan dan minuman terbesar di dunia, berhasil menurunkan tingkat cacat produknya sebesar 50% setelah menerapkan TPM. Hal ini memungkinkan perusahaan untuk meningkatkan kepuasan pelanggan dan memperkuat citra merek mereka.
- Pengurangan lead time: Procter & Gamble (P&G), perusahaan FMCG terkemuka asal Amerika Serikat, melaporkan pengurangan lead time hingga 70% setelah menerapkan TPM. Dengan demikian, perusahaan mampu memenuhi permintaan pasar secara lebih cepat dan meningkatkan pangsa pasar mereka.
Itulah beberapa contoh perusahaan global kelas dunia yang telah berhasil menerapkan Total Productive Maintenance (TPM) dan merasakan manfaatnya secara signifikan. Implementasi TPM yang sukses memang dapat memberikan dampak positif bagi industri manufaktur dalam meningkatkan efisiensi, mengurangi biaya, dan meningkatkan kualitas produk.
“Dapatkan solusi terbaik untuk meningkatkan kinerja dan hasil produksimu dengan implementasi Total Productive Maintenance bersama Senior TPM Consultant terakriditasi, dan raih kesuksesanmu sebagai pelaku bisnis yang handal!”
Contoh Kasus di PT. Manufaktur Sejahtera
Ini salah satu contoh yang terjadi pada klien kami. Sebut saja PT. Manufaktur Sejahtera, perusahaan yang bergerak di bidang produksi komponen otomotif.
Mereka menghadapi beberapa masalah dalam operasionalnya, seperti tingginya downtime mesin (sekitar 1500 jam per tahun), rendahnya efisiensi produksi (hanya 60%), tingginya biaya perawatan (Rp 500 juta per tahun), rendahnya kualitas produk (tingkat cacat 10%), dan panjangnya lead time (30 hari). Untuk mengatasi masalah ini, perusahaan memutuskan untuk menerapkan Total Productive Maintenance (TPM).
Problems:
- Downtime mesin yang tinggi, mengakibatkan kapasitas produksi yang rendah dan banyaknya waktu tidak produktif.
- Efisiensi produksi yang rendah, berdampak pada tingginya pemborosan sumber daya dan biaya produksi.
- Biaya perawatan yang tinggi, mengurangi laba perusahaan dan daya saing di pasar.
- Kualitas produk yang rendah, mengakibatkan kepuasan pelanggan yang buruk dan potensi kerugian bisnis.
- Lead time yang panjang, membuat perusahaan sulit memenuhi permintaan pelanggan secara tepat waktu.
Tahapan Solusi yang kami lakukan saat itu:
Pertama: Identifikasi dan analisis masalah: Tim manajemen PT. Manufaktur Sejahtera perlu mengidentifikasi dan menganalisis masalah yang dihadapi perusahaan secara menyeluruh. Ini melibatkan pengumpulan data dan informasi terkait downtime mesin, efisiensi produksi, biaya perawatan, kualitas produk, dan lead time.
Kedua, Pelatihan dan pembentukan Kaizen Team: Perusahaan perlu menyediakan pelatihan TPM dan Kaizen bagi seluruh karyawan dan membentuk Kaizen Team yang terdiri dari anggota dari berbagai departemen. Tim ini akan bertanggung jawab untuk mengawasi dan mengkoordinasikan implementasi TPM dan inisiatif perbaikan berkelanjutan (Kaizen) di seluruh perusahaan.
Ketiga, Pendekatan PDCA (Plan-Do-Check-Act): Kaizen Team akan menggunakan pendekatan PDCA dalam proses perbaikan.
Keempat, Standarisasi Proses: Setelah perbaikan berhasil, proses tersebut perlu distandarisasi dan diimplementasikan di seluruh perusahaan. Standarisasi akan membantu memastikan bahwa perbaikan yang dicapai dapat dipertahankan dan diterapkan secara konsisten.
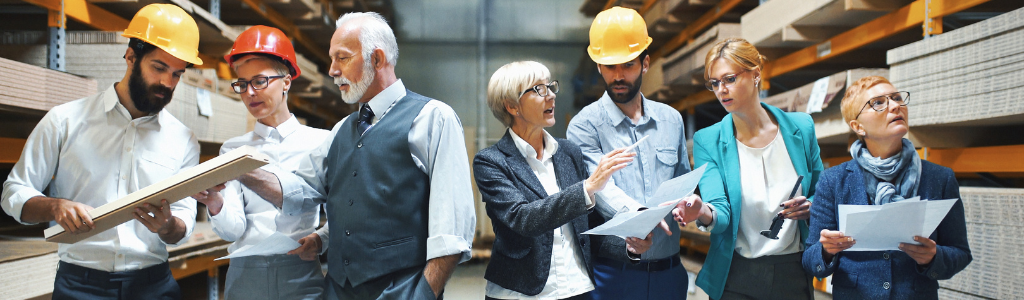
Contoh TPM dalam Industri Manufaktur, KAIZEN TEAM dan Tahapan PDCA
Berikut adalah contoh-contoh tahapan PDCA yang dilakukan oleh KAIZEN team:
Masalah: Downtime mesin yang tinggi
Plan:
- Mengidentifikasi penyebab downtime mesin.
- Menyusun rencana perbaikan, seperti pelaksanaan perawatan preventif dan peningkatan kompetensi operator.
Do:
- Melakukan perawatan preventif sesuai jadwal yang telah ditetapkan.
- Melatih operator mesin agar lebih ahli dalam mengoperasikan dan memelihara mesin.
Check:
- Memantau dan mengukur penurunan downtime mesin.
- Mengevaluasi efektivitas perawatan preventif dan pelatihan operator.
Act:
- Jika downtime mesin berhasil dikurangi, standarisasi prosedur perawatan preventif dan pelatihan operator.
- Jika belum berhasil, kembali ke tahap Plan dan ulangi siklus PDCA.
Masalah: Efisiensi produksi yang rendah
Plan:
- Mengidentifikasi penyebab rendahnya efisiensi produksi.
- Merancang rencana perbaikan, seperti mengurangi setup time dan mengoptimalkan layout pabrik.
Do:
- Menerapkan teknik setup time yang lebih cepat (misalnya, Single Minute Exchange of Die atau SMED).
- Mengoptimalkan layout pabrik untuk mengurangi waktu dan jarak transportasi bahan baku dan produk.
Check:
- Memantau dan mengukur peningkatan efisiensi produksi.
- Mengevaluasi efektivitas perbaikan yang telah dilakukan.
Act:
- Jika efisiensi produksi berhasil ditingkatkan, standarisasi embal setup time yang lebih cepat dan layout pabrik yang optimal.
- Jika belum berhasil, embali ke tahap Plan dan ulangi siklus PDCA.
Masalah: Biaya perawatan yang tinggi
Plan:
- Mengidentifikasi penyebab tingginya biaya perawatan.
- Menyusun rencana pengurangan biaya perawatan, seperti penerapan perawatan prediktif dan penggunaan suku cadang yang lebih tahan lama.
Do:
- Menerapkan perawatan prediktif dengan menggunakan teknologi pemantauan kondisi mesin.
- Mengganti suku cadang dengan yang lebih tahan lama dan berkualitas tinggi.
Check:
- Memantau dan mengukur pengurangan biaya perawatan.
- Mengevaluasi efektivitas perawatan prediktif dan penggunaan suku cadang yang lebih tahan lama.
Act:
- Jika biaya perawatan berhasil dikurangi, standarisasi perawatan prediktif dan penggunaan suku cadang yang lebih tahan lama.
- Jika belum berhasil, kembali ke tahap Plan dan ulangi siklus PDCA.
Masalah: Kualitas produk yang rendah
Plan:
- Mengidentifikasi penyebab rendahnya kualitas produk.
- Menyusun rencana per baikan, seperti penerapan sistem kontrol kualitas yang lebih ketat dan peningkatan kompetensi operator.
Do:
- Menerapkan sistem kontrol kualitas yang lebih ketat, seperti inspeksi di setiap tahap produksi dan penggunaan alat ukur yang lebih canggih.
- Melatih operator dalam hal kualitas dan pengendalian proses.
Check:
- Memantau dan mengukur peningkatan kualitas produk.
- Mengevaluasi efektivitas sistem kontrol kualitas yang lebih ketat dan pelatihan operator.
Act:
- Jika kualitas produk berhasil ditingkatkan, standarisasi sistem kontrol kualitas yang lebih ketat dan pelatihan operator.
- Jika belum berhasil, kembali ke tahap Plan dan ulangi siklus PDCA.
Masalah: Lead time yang panjang
Plan:
- Mengidentifikasi penyebab lead time yang panjang.
- Menyusun rencana perbaikan, seperti mengurangi waktu tunggu bahan baku dan meningkatkan koordinasi antardepartemen.
Do:
- Meningkatkan hubungan dengan pemasok untuk mengurangi waktu tunggu bahan baku.
- Meningkatkan koordinasi antardepartemen untuk memastikan kelancaran proses produksi dan pengiriman.
Check:
- Memantau dan mengukur penurunan lead time.
- Mengevaluasi efektivitas perbaikan yang telah dilakukan.
Act:
- Jika lead time berhasil dikurangi, standarisasi prosedur pengurangan waktu tunggu bahan baku dan koordinasi antardepartemen.
- Jika belum berhasil, kembali ke tahap Plan dan ulangi siklus PDCA.
Dengan menerapkan pendekatan problem solving PDCA yang dilaksankaan oleh Gugus KAIZEN TEAM dan standarisasi proses perubahan serta OPL bisa mengatasi masing-masing masalah, PT. Manufaktur Sejahtera. Dan ini dapat mencapai perbaikan yang signifikan dalam operasionalnya.
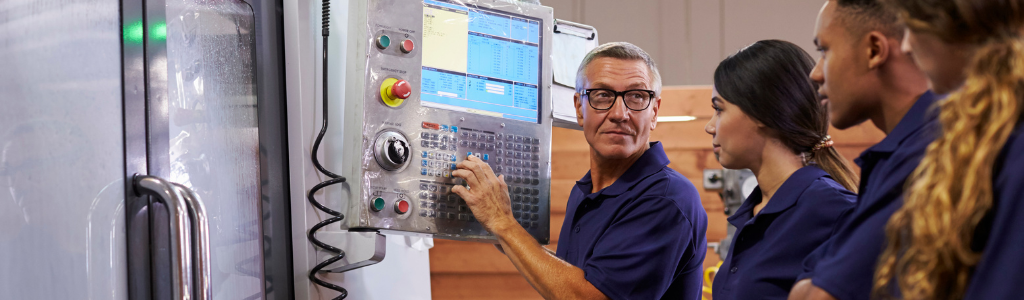
Contoh TPM dalam Industri Manufaktur, OPL – One Point Lesson
OPL (One Point Lesson) adalah metode pembelajaran singkat yang berfokus pada satu poin atau topik spesifik yang penting untuk pekerjaan sehari-hari. Tujuannya adalah untuk menyampaikan informasi penting secara sederhana dan mudah dipahami oleh karyawan dalam waktu yang singkat. OPL umumnya digunakan dalam industri manufaktur sebagai bagian dari pelatihan karyawan dan sebagai alat komunikasi dalam program perbaikan berkelanjutan seperti TPM (Total Productive Maintenance) dan Kaizen.
Tahapan OPL:
- Identifikasi topik: Tentukan topik atau poin penting yang perlu disampaikan kepada karyawan. Topik ini harus relevan dengan pekerjaan mereka dan dapat membantu mereka bekerja lebih efisien dan aman.
- Penyusunan materi: Susun materi OPL yang jelas, singkat, dan mudah dipahami. Materi ini harus mencakup tujuan, langkah-langkah yang perlu diikuti, serta gambar atau ilustrasi yang relevan.
- Penyampaian OPL: Sampaikan OPL kepada karyawan secara langsung, baik secara individual atau dalam kelompok kecil. Pastikan mereka memahami informasi yang disampaikan dan memberikan kesempatan untuk bertanya jika ada kebingungan.
- Evaluasi dan perbaikan: Setelah OPL disampaikan, evaluasi efektivitasnya dan buat perbaikan jika diperlukan. Ini bisa melibatkan menggabungkan umpan balik dari karyawan dan mengupdate materi OPL sesuai kebutuhan.
Implementasi OPL:
- Tentukan frekuensi penyampaian OPL, misalnya mingguan atau bulanan.
- Buat jadwal OPL yang sistematis dan konsisten agar karyawan tahu kapan dan apa yang akan dipelajari.
- Sampaikan OPL dalam lingkungan yang kondusif agar karyawan bisa fokus pada materi yang disampaikan.
- Gunakan alat bantu visual yang efektif, seperti papan tulis, flip chart, atau proyektor.
- Dukung OPL dengan dokumentasi yang mudah diakses oleh karyawan untuk referensi di kemudian hari.
Contoh implementasi OPL yang gagal dapat terjadi di tempat kerja ketika perusahaan tidak memperhatikan salah satu atau beberapa kesalahan di atas. Misalnya, sebuah perusahaan mengimplementasikan OPL untuk meningkatkan efisiensi operasional, namun tidak melibatkan tim dari departemen yang terkait, sehingga beberapa masalah terkait dengan proses operasional tetap tidak teratasi. Atau, sebuah perusahaan membuat OPL untuk meningkatkan produktivitas karyawan, namun tidak menentukan indikator kinerja yang jelas, sehingga tidak ada cara untuk mengevaluasi keberhasilan implementasi OPL tersebut.
Tips terbaik untuk implementasi OPL:
- Fokus pada satu topik: Pastikan OPL hanya mencakup satu topik atau poin penting agar karyawan tidak kelebihan informasi dan mudah memahami materi.
- Gunakan bahasa yang sederhana: Hindari jargon teknis atau istilah yang sulit dipahami. Gunakan bahasa sehari-hari yang mudah dimengerti oleh semua karyawan.
- Visualisasi: Gunakan gambar, diagram, atau ilustrasi yang relevan untuk membantu karyawan memahami konsep yang disampaikan.
- Praktik langsung: Jika memungkinkan, ajak karyawan untuk langsung mempraktikkan konsep yang dipelajari dalam OPL, sehingga mereka lebih mudah mengingat dan mengaplikasikannya dalam pekerjaan sehari-hari.
- Beri kesempatan untuk pertanyaan: Setelah menyampaikan OPL, beri kesempatan kepada karyawan untuk mengajukan pertanyaan atau klarifikasi. Hal ini akan membantu memastikan bahwa mereka benar-benar memahami materi yang disampaikan.
- Ulangi dan tinjau: Lakukan pengulangan OPL secara berkala untuk memastikan karyawan tetap mengingat materi yang telah dipelajari. Tinjau dan perbarui materi OPL jika ada perubahan dalam proses kerja atau teknologi yang digunakan.
3 Contoh OPL di tempat kerja:
#1. OPL: Pemeriksaan Mesin Secara Rutin Tujuan: Mengurangi downtime mesin dan mencegah kerusakan.
- Setiap operator mesin harus melakukan pemeriksaan visual mesin sebelum dan sesudah penggunaan.
- Operator harus melaporkan masalah atau kerusakan yang ditemukan kepada Kaizen Team.
#2. OPL: Pengaturan Bahan Baku Tujuan: Meningkatkan efisiensi produksi dan mengurangi pemborosan.
- Pastikan bahan baku diletakkan di tempat yang telah ditentukan dan mudah diakses oleh operator mesin.
- Gunakan sistem first-in, first-out (FIFO) untuk mengurangi risiko kerusakan bahan baku.
#3. OPL: Pemeriksaan Kualitas Produk Tujuan: Meningkatkan kualitas produk dan kepuasan pelanggan.
- Operator harus melakukan pemeriksaan kualitas produk secara berkala selama proses produksi.
- Jika ditemukan produk cacat, operator harus melaporkannya kepada Kaizen Team dan mengidentifikasi penyebabnya untuk segera ditangani.
Jadi, Dengan menerapkan TPM dalam Industri Manufaktur, Kaizen, pendekatan PDCA, dan standarisasi proses, PT. Manufaktur Sejahtera diharapkan dapat mengatasi masalah yang dihadapi dan meraih manfaat seperti penurunan downtime mesin, peningkatan efisiensi produksi, pengurangan biaya perawatan, peningkatan kualitas produk, dan pengurangan lead time. Dengan demikian, perusahaan dapat menjadi lebih kompetitif di pasar, meningkatkan kepuasan pelanggan, dan mencapai pertumbuhan yang berkelanjutan. Semoga PT. Manufaktur Sejahtera sukses dalam menerapkan TPM dan Kaizen, serta dapat meraih hasil yang memuaskan dari perubahan ini.
Selamat mencoba, dan sampai jumpa di pembahasan menarik lainnya!
Dan Anda bisa terus belajar bersama dengan kami di Jago Kaizen dan Coach Wang.
Ingin mempelajari secara langsung dan privat dari Senior Konsultan TOTAL PRODUCTIVE MAINTENANCE?
Anda ingin mengundang trainer atau consulting provider?
PT Mitra Prima Produktivitas adalah provider coaching, mentoring, training, dan consulting ternama di Indonesia untuk kinerja Produktivitas dan peningkatan Profitabilitas.
Bersama Coach Wawang